So...., back to saving my buddy 20 bux... (Been on the back burner since the last time I annoyed you guys. LOL )
I actually managed to salvage the bearings and seals on the 350 that I'm also trying to salvage as economically as possible. Had one helluva time getting the bottom end to seal, tho..., even after grinding down the ends of the fasteners just to have that covered. Getting the previous pinches in the bearing holders lined back up with the seam between the cup and case when there's Dirko smeared all over em was the tricky part. Took a few stabs at it but the case held pressure all night. Still has a very small vac leak which doesn't seam to be the crank seals according to the grease test. About the only other place flexible enough to seal with pressure but leak with vac would be the impulse arrangement unless I'm overlooking something else. Think I'll see how it runs before chasing it too much further since it does hold at 4 ~ 5 inHg which
should be enough to run the pump diaphragm. (Not sure what that spec would be if there even is one.) I actually did think about using a little Dirko for the impulse connections but felt I had a good fit without it and have never had any issues with these before. Anyone use sealant for these impulse connections?
Otherwise another successful intake bulkhead 'trim and fit' with a universal CV joint clamp. Works like a charm every time and is so butt simple it's stupid. (Yeah, right up my alley!) My last clamp or I'd go ahead and cut it off and smear some goo on the impulse connection to the intake flange just because.
And speaking of bottom end leaks on these and bearing cover pinches,
@Tor R posted this pic on Sawhawgz. It's a modification to the older cups to allow the bearing cover some pinch space so the surfaces properly seal instead of actually having a gap due to the rubber bunching up or squeezing out between the cup and case. There's still enough surface beside the bevel on the outside for a good seal, but also some room for the bearing cover rubber to squeeze out instead of bunching up. (The case also needs the corresponding mod.) Evidently the design was eventually changed to reflect this, but earlier saws suffered leaks as a result of the issue. Was wondering if anyone has tried this or has noticed the differences between earlier and later versions of the cups and cases. Apparently the issue wasn't corrected until 2001, so that leaves quite a few of these saws out there that could possibly benefit from this simple mod. Maybe Tor will chime in with some additional info. Certainly worth checking your next 340/345/350 rebuild to see what you have and whether it could possibly benefit from this simple modification. Probably also worth checking any aftermarket bearing cups you may get with some of the rebuild kits.
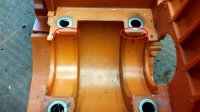