I am not going to pretend I know best here for one second, so please dont take it as such. I consider myself the saw novice here.
I was trained to rebuild electrical motors and they are actually very similar to a saw in the way the bearings mount and locate the main drive part centrally within the case..
Here is what I was taught.
The electric motor has a rotor which must be correctly centered to stop it running with any lateral force exerted on the bearings which kills them, similar to a crank.
Most electric motors, like most saws, have a non drive end (flywheel side) where the bearing goes in and has a machined end where the bearing will seat up against. This is called the locating bearing and with the bearing seated up against the shaft stop, should hold the rotating center where it is supposed to be.
I was taught that this end should always be assembled first by putting the bearing on the shaft to its mounting shoulder, and then in the housing to locate the motor shaft where it needs to be.
The dive end is different. It does not matter where it is located in the housing which is why the bearing is sometimes larger. Its job is to take the load or radial force. As long as it is mounted up against the shaft shoulder for stability, its good.
The thought of using the oil pump as a seating stop screams against everything I was taught. It could be an after market pump with slightly different dimensions which will not seat the bearing up against the crank shaft shoulder properly.
This would destroy an electric motor's bearings very fast due to the magnetic force pulling against the bearing laterally to correct the center rotor misalignment, but it can probably be gotten away with in a saw as the force is all radial (up and down). So as long as the crank is center enough and there is enough lateral play in the piston to allow it to center its self, it will work fine.
Not ideal but it will work.
Now as I said..... I am not 2 stroke expert but I have been trained in how to install and work with bearings to make them last.
When I do anything I think of what forces are being put where and if it dont spin freely when assembled, something is wrong.
The way I described assembling above will pinch the drive side bearing a bit tight when the case halves are tensioned together, but a light tap (which is unfortunately not as easy on some saw models as it is on an 1122 Stihl) will push the upper bearing race back over and center it.
This saw went together tight and with one tap of the punch as shown below, the crank latterly rolled and dropped to it its low gravity center by its self, and spun with no restriction.
I wont continue unless I have this state.
I dont want to tell any of the more experienced folks here how to do things as I am learning, but just want to share my thoughts and knowledge.
100% happy to be corrected on any of my thoughts above when it comes to putting a saw together, I encourage it!
I hope this helps a bit.
One of the bearing races will need to be tapped in or out to release the pressure.
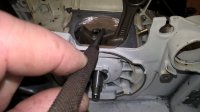