You just made things SO easy for me, thanks a ton I'm fine with a ton of cleanup (or ugly results) was just hoping my torches could work w/ something, feel stupid buying a welding setup to make mufflers
How strong a bond does this make, would it be adequate to hold a "shotgun type exit" if the exit-tube itself got a good deal of this flux/solder/braze on both sides, as it were?
Thanks again, am embarrassed to even show how mine look due to using nuts&bolts for my deflectors but my thinking is their "turbulence induction" is basically irrelevant, will explain since it's easier than showing pics (they don't convey what my goal is)
With any muffler my goal is for the charge to leave the exhaust port and expand as much as possible before having a chance to exit, with the intention of causing the exhaust pulse to leave the flange and either "swing back" at the flange or, failing that (which is more common given normal muffler design), the goal is to simply ensure there's high pressure by the flange.
Reasoning is that, since we can't use acoustic of pipes, we should at least capitalize/optimize the
other prime purpose of a pipe which is pressurization to eliminate excess charge spill-out, am betting this is precisely why the 660 muffler for example does not want front cover exits, it's better to have the entire force of that exhaust pulse "mushroom" into the front and curve back, seeking the primary exit which
forces the exiting air right by the flange.... My next 660 muffler, instead of making an extra hole on the side opposing the primary hole, instead I'll be lengthening (rear-wards) the primary hole, into an oval, and - if this brazing is strong enough - will affix a pipe there, not a 4" or anything just something bigger than a deflector I just want a lil bit of pressure "at the exit" or "in the exit" so to speak.
Should note that this type of approach is how I do every single one of my mufflers, usually I'm able to follow the OEM layout, roughly at least, and simply "open up" things, and IMO following the OEM is usually best (unless you're good at making short pipes, I am obviously not!), with a mindset that it's important to under-do it since you cannot expect to hit 'optimal' and you lose power pretty quick with oversized exits (but don't gain a ton by, say, going from 95% optimum to 100%....but going to 105% you take a substantial loss, if that makes sense?)
Echo 590 muffler, top cover patched-over because the 'exit tube' can't be "over-bored" to allow adequate flow, but I did use that area to go in and open up the holes in the baffle so the front-to-back passthrough was way higher (focusing, of course, on upper/outer holes as to avoid primary exhaust pulse force) Then made pair of exits on the upper front cover, around 55% or 60% of exhaust flange would have to check my notes but erred to smaller side and always go with 2 when I have the choice because I'd swear it sounds better, but on say a 660 I'd simply be enlarging the OEM primary hole because I'd want to force as much exiting gas as possible past that exhaust flange
Ok fine one of the ridiculous nuts&bolts "dual port" 660's
2511t, I had made my new exit-enlargement on the far-left, so that I could reach the OEM baffles (3 holes in the OEM wall of regular, non-cat 2511 muffler, gas enters rear, expands on far-side's rear chamber and passes (3) baffle holes here into front portion), now that I have that brazing trick I'll be patching-up the left-side hole entirely and simply expanding the OEM hole

Figured to show this since most seem to ignore the flange-to-muffler area, which is not just a sharp 90deg bend but also a choke-point and tons of sharp-edges, can gain nearly 20% throughput while smoothing/flowing the turn:
And since I've never seen others do this, and it's worked well for long enough for me now, I use Motoseal as a "heat shield paint" on the inside faces of plastic muffler guards, the muff-sides of clutch covers, under the mufflers on 660's/590's/etc types, have only burnt
some off one saw so far and it's my 355t where the muff is true(stupid) "open can" because they(Echo) just make it so easy on that model, I didn't know better and "it worked" so I've yet to do better, just leave it full open lol (runs an 18" awesome to this day

)
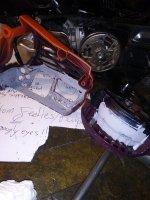