paragonbuilder
Mastermind Approved!
- Local time
- 3:35 PM
- User ID
- 384
- Joined
- Jan 2, 2016
- Messages
- 9,229
- Reaction score
- 33,868
- Location
- Norwich, CT

I'm anxious to see a particular saw on it.
2 saws actually.
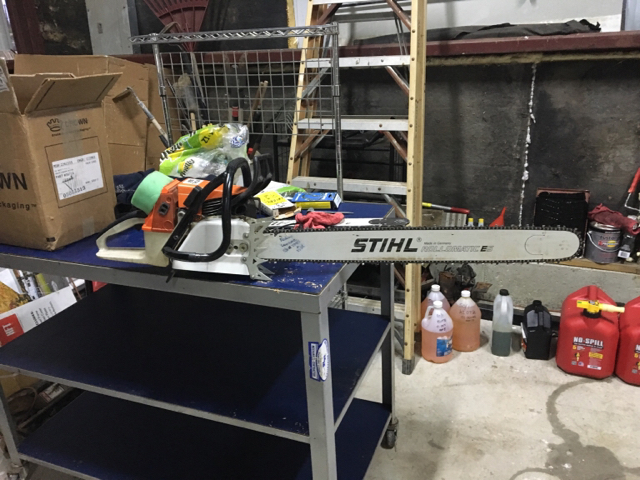
This one?
I'm anxious to see a particular saw on it.
2 saws actually.
If you mean peak I think that is just where that saw was tuned to. You can see no load at 12,500 when no brake was being applied, than again where it has a load at the same rpm.Any reason the RPM range is lower than I would have expected?
Any reason the RPM range is lower than I would have expected?
Hey Mike-
Bill's Makita was only taching to about 12500 that day we both thought she was running rich. We start data collection when he's at full throttle and hits the brake to make the torque go up over a threshold you can set in the parameters and then collection stops when the torque drops below the stop threshold. Usually it will stop when the brake is let go which could be at a higher RPM than you want -- but Bill had a good run here on the low side and brought her down to 7000. Most guys probably wouldn't lug a saw much below 7000 when cutting regularly (I think!).
This one had peak HP at 9000 RPM with 6.4 HP.
What will be cool as long things hold together is we could turn the H needle in an 1/8 and run it again, check graph (instantly), turn the needle again, run, check graph... it grabs the runs very easily.
If we ever do a hydraulic setup I'm hoping to use a stepper motor or servo to let the computer control the needle valve -- then the computer could turn the needle valve at a rate that drops the RPMs as evenly as possible over time -- just like a car dyno. Am I right that car dynos usually control the throttle so the RPMs go up at even intervals? I have no experience running any off the shelf dynos.
Any reason the RPM range is lower than I would have expected?
Yes, you are right. Most professional dynos have a PID controller for an "auto load valve". In the software you target a RPM rate of change, usually 200-500 RPM/s, and the software takes over the load valve after you've armed it and hit WOT. It will go to zero load and release control of the valve as soon as you back off the throttle.
Hey Shaun -- yeah PID control came to mind when I thought about how the computer would need to react to the RPM changing to target an RPM decel rate. Could have a parameter for RPM decel rate (RPMS per second I guess) create a profile and run a PID loop based on RPM feedback and slow down or speed up the needle valve stepper / servo to try and stay on profile. Now we're gettin' complex... but hey why not? we've got the compute power in these cheap lower power toys. This is the type of stuff we're doing with the linear motors that is my day job.
I gotta get off the forum and go get ready to head to Dan's... Yikes.
Software nerd but it's weekend warrior cutting time... with a bunch of great guys at the CT GTG!
A tool like this would be very handy to have in the shop, it takes the "it feels faster " out.I suggest a disclaimer, you put your saw on this mowshin. its public info. We are trying to figure out how to tune these motors. they are getting stronger because we discuss the good bad and ugly. Thanks to mopar, al and jason and anyone I may have forgotten for being open to share their runs and their build specs.
My pleasure Sir.I suggest a disclaimer, you put your saw on this mowshin. its public info. We are trying to figure out how to tune these motors. they are getting stronger because we discuss the good bad and ugly. Thanks to mopar, al and jason and anyone I may have forgotten for being open to share their runs and their build specs.