malk315
Running Saws for Therapy
- Local time
- 5:37 AM
- User ID
- 421
- Joined
- Jan 6, 2016
- Messages
- 2,101
- Reaction score
- 10,140
- Location
- Lancaster, MA

Since the cat came out of the bag in the Upstate NY GTG thread here's the promised thread about the saw dyno with some video, pictures, and screenshots for you to check out.
wcorey (Bill) and myself (Eric) did the work along with a lot of discussion between paragonbuilder (Dan), drf255 (Al), Derf (Fred), and Mastermind (who the hell is Mastermind?). I also revealed to Mattyo that we were working on this to be used at the upcoming CT GTG. Bill showed the mechanical setup to some of you at the NY GTG.
Bill did all of the mechanical work and I did the electronics for it -- it reads and records several samples of RPMs and torque with magnets and Hall Effect Sensor on the shaft and a load cell that does 1 oz resolution driven by the 1 foot arm as the motorcycle caliper grabs the brake rotor. The data is recorded in RAM and written to flash when a run is complete. You can then graph or download the files and plot in excel or whatever tool you want. It has wifi and can be controlled via web interface with computer, phone, tablet wirelessly.
Uses a microcontroller style platform and its in an enclosure very low power. When done you will be able to run on AC brick or connect to 12V car battery.
Plan to keep working on it til it's usable by everyone (as easy and automated as possible).
Been working on this since CT GTG back in November! Really enjoy this stuff and the hardware/software for it is where I can contribute best.
Here is the obligatory video of the dyno in action with Bill's stock 372XP:
And a closeup shot of the electronics box:
The upper red display is for RPM, the middle for torque, and the lower for HP.
The compute platform is known as a "Beaglebone Black" which is a small microcontroller style ARM based embedded computer that runs Linux. The 3 displays run on SPI and as many as you want can be chained together. The HES sensor is fed into the hardware encoder high speed counter the CPU has and it can count up to a 100 mhz clock -- with saws up to 15K RPM we're down in the khz range so no problem (although Al's been known to have some serious RPM saws we might be in trouble!
JK.
The Load cell is beam style and can handle up to 20 Kg. It is sampled with a small 16 bit AtoD with built in gain amp perfect for reading load cells and talks to the bone with I2C. The beaglebone is on the left -- the blue light at the bottom is the WIFI dongle and it acts as an AP called "sawdyno" you can just point your phone or computer at and I've got a web interface to control it. The breadboard on the right has a level shifter at the top to shift the 3.3v bone logic to 5v the SPI displays need, the bottom right is the AtoD board for the load cell, and the bottom left there is a green LED that blinks when magnets go by the HES so you can visually make sure the HES is positioned properly to pickup the magnets. There is DIP style chip level shifter above that to take the HES from 5v to 3.3v logic for the bone and finally a low pass Resistor/CAP filter on the HES input as I was picking up noise from the SPI clock on the HES input.
The hardware is working great -- down the road I plan to have a hardware buddy create a PCB board of the breadboard components that will plug right in as a "cape" on the beaglebone. I've done that w/ other projects in the past. We also may investigate cost reduction by using a Raspberry PI platform although this isn't uber expensive -- about $50 for the bone and another $40 or $50 for the rest of the parts. We could probably get total cost to $50 or less if guys want a "kit" to make electronics for their own dynos and I can help w/ getting software and hardware setup. Should be able to attach these to any dyno that spins a shaft and pushes on something -- like the hydraulic one Chad did.
If you add all of the above up I've got logic that currently reads the RPMs and load cell every 0.1 seconds when doing a "run" with a saw and saves it in comma delimited format. It uses timed based runs for now but plan to switch to auto detecting a load / RPMs and recording the power curve. The web interface can show instantaneous graphs of the data or you can download the data and load into Excel or whatever graphing software and create plots.
Here's a picture of the load cell and a shot of it clamped to the bench w/ calibration weights on it:
The web interface can be used over the wireless -- here is the page that lets you configure a bunch of parameters needed at least to run it the style that Bill has created with a saw and shaft sprocket that create mechanical advantage -- this has to be converted from shaft RPM and torque to saw RPM and torque which is easy to do knowing the saw sprocket pin count and shaft sprocket pin count. When you guys want to try 7 pin vs. 8 pin rim sprockets the difference is accounted for. Bill's drive sprocket has 35 drive links so w/ a 7 pin rim sprocket its and multiplier of 5. I support showing shaft or saw RPMs / torque which is just a multiply by 5 for the RPMs and a divide by 5 for the torque. When you put your 8 pin on there, change saw sprocket pin count to 8 and have at her.
Jeremy -- when putting the web interface together I used the two idiots logo and was hoping you'd be OK with it on there. If you would rather us not use that logo I will replace it with something else just say so. My apologies for this appearing w/o you seeing it first. Just say the word if you'd rather it not be on there no worries at all.
The load cell is very linear and good through about 45 lbs (20 kg). You can calibrate it easily on this screen by putting a known weight in ounces on it and hit calibrate to get ozs per digital unit from the 16 bit AtoD. You can also zero it -- needed to on the original setup when some gravity from the brake would rest on the load cell and put some load on it. It zeros out nice.
Here is an interim graph -- with more magnets on the shaft we'll get finer RPM resolution and we're working on getting rid of the spikes from the load cell. The grabbiness of the brake, vibration, etc. have made it a bit all over the place. I'm going to sample the load cell at 10x more often and do a decimation filter in software so the 0.1 second updates are much cleaner (take 10 x 10 millisecond samples and use 10% of each to contribute to the 0.1 second update. It works great in trimming digital signals that are like that). We have also been trying some mechanical changes:
The above has time from 0 to 30 second on the horizontal and RPM plotted with torque and HP.
I'm hoping once we get the load cell noisiness out of there it will be clean enough for someone to see the HP/torque curves as obvious. I did take one plot in excel and did a proper least squares style curve (2nd order polynomial in Excel) to make it easy to see the curves -- hoping to get it there w/o the post processing needs. It won't let me attach anymore pictures so I'll show that in the next post to this thread. I'll also post more pictures of Bill's mechanical setup and some more videos we shot of his 372XP and my 372XP X-torq saw. The saw on the still shots is Bill's MS-440.
Hoping to make this thing usable by all (it may not be as simple as your i-phone but I'm going to do what I can to get as close as I can!).
We are hoping to have it rather usable by the CT GTG coming up on May 7th.
If you can make it to that GTG (it was a blast last November -- Dan / Mels / Cindy did a great job and great support from all who came) you can get a first hand view of we are with this thing.
My apologies for all of the technical crap. I figure maybe some of you guys that are into tech might have questions so I tried to answer.
After the GTG I plan to keep working on it and improving it. So far the numbers have been VERY reasonable as to where they should be -- around 4.5 HP for stock 372 and the RPMs are confirmed accurate via tach and math etc. If we get her further dialed in, saw builders could make some good use of it, that's the goal!
More in the next post now that the thread is started.
wcorey (Bill) and myself (Eric) did the work along with a lot of discussion between paragonbuilder (Dan), drf255 (Al), Derf (Fred), and Mastermind (who the hell is Mastermind?). I also revealed to Mattyo that we were working on this to be used at the upcoming CT GTG. Bill showed the mechanical setup to some of you at the NY GTG.
Bill did all of the mechanical work and I did the electronics for it -- it reads and records several samples of RPMs and torque with magnets and Hall Effect Sensor on the shaft and a load cell that does 1 oz resolution driven by the 1 foot arm as the motorcycle caliper grabs the brake rotor. The data is recorded in RAM and written to flash when a run is complete. You can then graph or download the files and plot in excel or whatever tool you want. It has wifi and can be controlled via web interface with computer, phone, tablet wirelessly.
Uses a microcontroller style platform and its in an enclosure very low power. When done you will be able to run on AC brick or connect to 12V car battery.
Plan to keep working on it til it's usable by everyone (as easy and automated as possible).
Been working on this since CT GTG back in November! Really enjoy this stuff and the hardware/software for it is where I can contribute best.
Here is the obligatory video of the dyno in action with Bill's stock 372XP:
And a closeup shot of the electronics box:

The upper red display is for RPM, the middle for torque, and the lower for HP.
The compute platform is known as a "Beaglebone Black" which is a small microcontroller style ARM based embedded computer that runs Linux. The 3 displays run on SPI and as many as you want can be chained together. The HES sensor is fed into the hardware encoder high speed counter the CPU has and it can count up to a 100 mhz clock -- with saws up to 15K RPM we're down in the khz range so no problem (although Al's been known to have some serious RPM saws we might be in trouble!

The Load cell is beam style and can handle up to 20 Kg. It is sampled with a small 16 bit AtoD with built in gain amp perfect for reading load cells and talks to the bone with I2C. The beaglebone is on the left -- the blue light at the bottom is the WIFI dongle and it acts as an AP called "sawdyno" you can just point your phone or computer at and I've got a web interface to control it. The breadboard on the right has a level shifter at the top to shift the 3.3v bone logic to 5v the SPI displays need, the bottom right is the AtoD board for the load cell, and the bottom left there is a green LED that blinks when magnets go by the HES so you can visually make sure the HES is positioned properly to pickup the magnets. There is DIP style chip level shifter above that to take the HES from 5v to 3.3v logic for the bone and finally a low pass Resistor/CAP filter on the HES input as I was picking up noise from the SPI clock on the HES input.
The hardware is working great -- down the road I plan to have a hardware buddy create a PCB board of the breadboard components that will plug right in as a "cape" on the beaglebone. I've done that w/ other projects in the past. We also may investigate cost reduction by using a Raspberry PI platform although this isn't uber expensive -- about $50 for the bone and another $40 or $50 for the rest of the parts. We could probably get total cost to $50 or less if guys want a "kit" to make electronics for their own dynos and I can help w/ getting software and hardware setup. Should be able to attach these to any dyno that spins a shaft and pushes on something -- like the hydraulic one Chad did.
If you add all of the above up I've got logic that currently reads the RPMs and load cell every 0.1 seconds when doing a "run" with a saw and saves it in comma delimited format. It uses timed based runs for now but plan to switch to auto detecting a load / RPMs and recording the power curve. The web interface can show instantaneous graphs of the data or you can download the data and load into Excel or whatever graphing software and create plots.
Here's a picture of the load cell and a shot of it clamped to the bench w/ calibration weights on it:
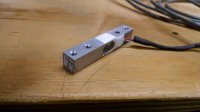
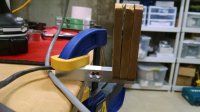
The web interface can be used over the wireless -- here is the page that lets you configure a bunch of parameters needed at least to run it the style that Bill has created with a saw and shaft sprocket that create mechanical advantage -- this has to be converted from shaft RPM and torque to saw RPM and torque which is easy to do knowing the saw sprocket pin count and shaft sprocket pin count. When you guys want to try 7 pin vs. 8 pin rim sprockets the difference is accounted for. Bill's drive sprocket has 35 drive links so w/ a 7 pin rim sprocket its and multiplier of 5. I support showing shaft or saw RPMs / torque which is just a multiply by 5 for the RPMs and a divide by 5 for the torque. When you put your 8 pin on there, change saw sprocket pin count to 8 and have at her.
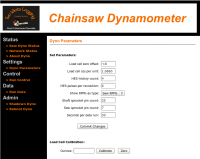
Jeremy -- when putting the web interface together I used the two idiots logo and was hoping you'd be OK with it on there. If you would rather us not use that logo I will replace it with something else just say so. My apologies for this appearing w/o you seeing it first. Just say the word if you'd rather it not be on there no worries at all.
The load cell is very linear and good through about 45 lbs (20 kg). You can calibrate it easily on this screen by putting a known weight in ounces on it and hit calibrate to get ozs per digital unit from the 16 bit AtoD. You can also zero it -- needed to on the original setup when some gravity from the brake would rest on the load cell and put some load on it. It zeros out nice.
Here is an interim graph -- with more magnets on the shaft we'll get finer RPM resolution and we're working on getting rid of the spikes from the load cell. The grabbiness of the brake, vibration, etc. have made it a bit all over the place. I'm going to sample the load cell at 10x more often and do a decimation filter in software so the 0.1 second updates are much cleaner (take 10 x 10 millisecond samples and use 10% of each to contribute to the 0.1 second update. It works great in trimming digital signals that are like that). We have also been trying some mechanical changes:
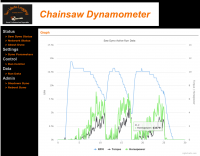
The above has time from 0 to 30 second on the horizontal and RPM plotted with torque and HP.
I'm hoping once we get the load cell noisiness out of there it will be clean enough for someone to see the HP/torque curves as obvious. I did take one plot in excel and did a proper least squares style curve (2nd order polynomial in Excel) to make it easy to see the curves -- hoping to get it there w/o the post processing needs. It won't let me attach anymore pictures so I'll show that in the next post to this thread. I'll also post more pictures of Bill's mechanical setup and some more videos we shot of his 372XP and my 372XP X-torq saw. The saw on the still shots is Bill's MS-440.
Hoping to make this thing usable by all (it may not be as simple as your i-phone but I'm going to do what I can to get as close as I can!).
We are hoping to have it rather usable by the CT GTG coming up on May 7th.
If you can make it to that GTG (it was a blast last November -- Dan / Mels / Cindy did a great job and great support from all who came) you can get a first hand view of we are with this thing.
My apologies for all of the technical crap. I figure maybe some of you guys that are into tech might have questions so I tried to answer.
After the GTG I plan to keep working on it and improving it. So far the numbers have been VERY reasonable as to where they should be -- around 4.5 HP for stock 372 and the RPMs are confirmed accurate via tach and math etc. If we get her further dialed in, saw builders could make some good use of it, that's the goal!
More in the next post now that the thread is started.