- Local time
- 10:00 AM
- User ID
- 297
- Joined
- Dec 28, 2015
- Messages
- 5,194
- Reaction score
- 34,214
- Location
- Central Ohio

So Day Two of my puzzlement 
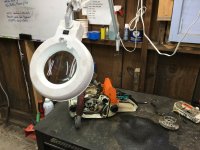
Day one back here for those who want to catch up on my failure
http://opeforum.com/threads/064-pipe-saw.3011/page-2#post-133905
With the coil removed the crank spun freely.
I removed the flywheel again and don't see any marks to show me if it had abnormal timing in the past.
It initially looked like the crank was bent but I was getting deceived by a dent on the tip of the crankshaft that made it look like it wasn't spinning true.
I pulled the clutch and found this.
remember to pull the brass sleeve carefully from the oil line before removing the oil pump so the cast nipple doesn't brake off, you can pry it out pretty easily with the long handle tuning screwdriver, the little freebie one that we all have tons of isn't the right shaped tip for this though.
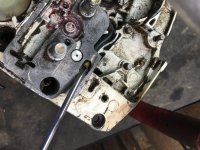
But looking at both ends the crank seems fine and to spin true without wobble.
As far as signs of previous crank modifications all I noticed was the bottom of the big end bearing boll seems to have an odd texture to the metal. I compared to a handful of other 064 cranks I have and none have this texture/finish.
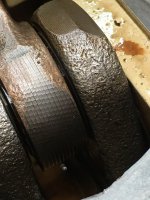

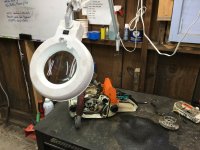
Day one back here for those who want to catch up on my failure

http://opeforum.com/threads/064-pipe-saw.3011/page-2#post-133905
With the coil removed the crank spun freely.
I removed the flywheel again and don't see any marks to show me if it had abnormal timing in the past.
It initially looked like the crank was bent but I was getting deceived by a dent on the tip of the crankshaft that made it look like it wasn't spinning true.
I pulled the clutch and found this.
remember to pull the brass sleeve carefully from the oil line before removing the oil pump so the cast nipple doesn't brake off, you can pry it out pretty easily with the long handle tuning screwdriver, the little freebie one that we all have tons of isn't the right shaped tip for this though.
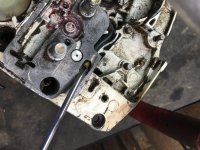
But looking at both ends the crank seems fine and to spin true without wobble.
As far as signs of previous crank modifications all I noticed was the bottom of the big end bearing boll seems to have an odd texture to the metal. I compared to a handful of other 064 cranks I have and none have this texture/finish.
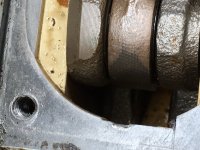
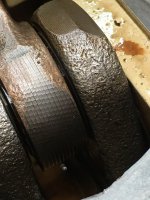