markds2
Here For The Long Haul!
- Local time
- 7:38 PM
- User ID
- 6804
- Joined
- Jul 22, 2018
- Messages
- 995
- Reaction score
- 5,825
- Location
- Nelson, New Zealand

I have been very hesitant to post this, but as it is the second 084 I've found with exactly the same fault I felt it my duty (and I was encouraged to by another member) to post about it, as it may help others solve the same issue - as it stands to reason that if I've found it on two 084's there may be more out there like it!
Background to the story is that I was sent this early 084 (it has the early unlimited coil with the separate trigger) over a year ago, with the owner complaining that the oil pump was, and had always been, very anemic with between a 1/4 and 1/3 of a tank of oil being used for every tank of fuel. He did mention that it poured oil out when he held in the auxiliary button (but who wants to do that all the time), but with the pump adjusted to maximum it had very poor flow, and could hardly oil a 30-inch bar. I got the saw and carefully inspected the pump, and it looked to be in perfect condition internally, I did all the seals and O-rings and replaced the hard black tube that routes the oil from the pump to the bar pad (someone had used tygon fuel hose!). I tested the saw, and it seemed to oil OK when just eyeballing the flow from the bar pad, so I sent it back to him.
He soon complained that oil flow was no better, and in the meantime, I found that my own ported o84 (which is considerably newer - going by serial numbers) exhibited the exact same symptoms, the pump would work, but the flow was useless. So back in September I dismantled the pump and found the following fault, which has to be from the factory. The pictures below are from the first 084 (which my customer sent back to me), which exhibits the exact same manufacturing fault as mine:
To understand properly, first I need to explain how the pump works. The following picture shows the pump piston, which, as it is spun, moves in and out, through the action of the 'ramp' on the RH end.
You can see the ramp through the hole where the control bolt is meant to reside:
And again here, looking at the end of the pump, with the control bolt in place:

Background to the story is that I was sent this early 084 (it has the early unlimited coil with the separate trigger) over a year ago, with the owner complaining that the oil pump was, and had always been, very anemic with between a 1/4 and 1/3 of a tank of oil being used for every tank of fuel. He did mention that it poured oil out when he held in the auxiliary button (but who wants to do that all the time), but with the pump adjusted to maximum it had very poor flow, and could hardly oil a 30-inch bar. I got the saw and carefully inspected the pump, and it looked to be in perfect condition internally, I did all the seals and O-rings and replaced the hard black tube that routes the oil from the pump to the bar pad (someone had used tygon fuel hose!). I tested the saw, and it seemed to oil OK when just eyeballing the flow from the bar pad, so I sent it back to him.
He soon complained that oil flow was no better, and in the meantime, I found that my own ported o84 (which is considerably newer - going by serial numbers) exhibited the exact same symptoms, the pump would work, but the flow was useless. So back in September I dismantled the pump and found the following fault, which has to be from the factory. The pictures below are from the first 084 (which my customer sent back to me), which exhibits the exact same manufacturing fault as mine:
To understand properly, first I need to explain how the pump works. The following picture shows the pump piston, which, as it is spun, moves in and out, through the action of the 'ramp' on the RH end.
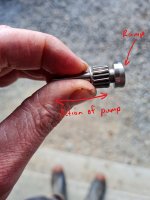
You can see the ramp through the hole where the control bolt is meant to reside:
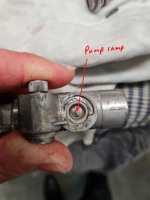
And again here, looking at the end of the pump, with the control bolt in place:
