BuffaloBill
Well-Known OPE Member
- Local time
- 5:26 PM
- User ID
- 20843
- Joined
- Nov 27, 2021
- Messages
- 26
- Reaction score
- 100
- Location
- Wisconsin

I don’t have a real need for more chainsaws but enjoy engines in general and wanted this experience. I’d watched a few eBay auctions and Facebook marketplace adds for a genuine Stihl 200T, but they‘re asking too much IMO. So when I saw a “sale” price on an orange parts kit I ordered one.
I have no prior porting experience, but have enjoyed reading all the information shared here and on YouTube and wanted to give it a go. I do have a lathe & mill and liked the idea of raising compression by lowering the cylinder and cutting squish to some minimal dimension. Will these low cost components stand up to high compression, etc., I don’t know….. I’d come across a few of you experienced builders who shared numbers, and set out to replicate port timings that Mastermind shared in a post a number of years ago (102, 126, 81.X).
Stock numbers w/o base gasket measured 98, 130.5/133, 77.5, squish .036. I took .036 off the cylinder base and landed on Mastermind’s timing numbers. I then made a squish cutting tool and sanding drum as Treemonkey showed in a video (thanks Treemonkey, I’m about 60miles south west of you). And even though I was cautioned to not create a ridge that can falsely show a big squish reading, I let it happen. I hadn’t ground enough relief at the end of my tool bit. By the time I corrected that and got the ridge cut out, I was right back at the stock .036” squish.…..
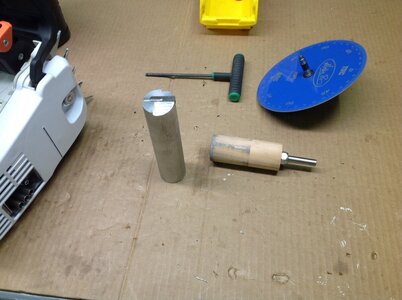
So I took another .019” off the base, knowing the intake duration would end up greater than the target, but I figured I had really nothing to loose and experience to gain. Not wanting to recall the math needed to calculate port height vs degrees, I made a simple model in Solidworks using the stroke and rod length. From this model I determined the primary and secondary transfers should be raised .089 and .079 respectively, to land on 126/129 degrees.
The open transfer design allowed me to grab the cylinder upside down in the mill vice and accurately cut them “deeper” (and keep them flat) by those dimensions, using a 1/4” carbide end mill. I attempted to blend the remaining step into the corners of the transfer ports, making a small radius there with an 1/8” dremel bit (I hated to show pic of this work!). I raised the exhaust a bit and slightly widened the exhaust and intake to end up with these timing numbers:
EX 102
pri 126
sec 130
IN 82.5
I, more carefully this time, cut the squish to .019”. The muffler outlet I made with 3/8” OD tubing. I used three of these outlets to land on a combined area I’m hoping will run well. I have not yet measured compression, but am guessing it’s fairly high. Piston is a Hyway pop-up. I have no bar yet so only ran it w/o load this morning. The throttle response seems good and it is “very angry” in nature. Am looking forward to getting it in some wood.
Possible concerns:
Will the cheap crank ass’y and bearings take it?
After removing .055” from the cylinder base, the flange thickness is only .155”. Will it fracture there?
Is the resulting 165 degees intake duration likely to cause poor performance and/or waste fuel?
Is the width of the squish band too great (or the dome volume too small)?
Will I be sucked into yet another hobby where no number of chainsaws will ever be enough?
Thanks for reading!
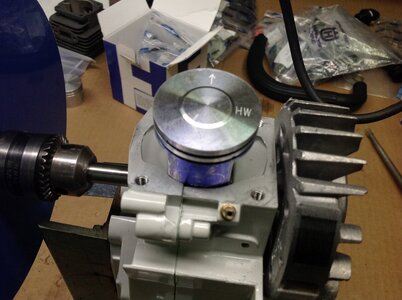
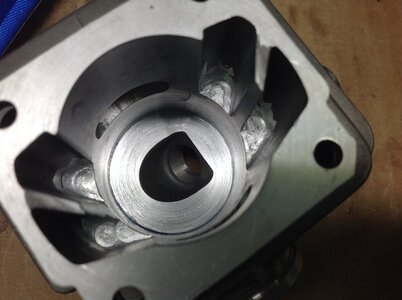
I have no prior porting experience, but have enjoyed reading all the information shared here and on YouTube and wanted to give it a go. I do have a lathe & mill and liked the idea of raising compression by lowering the cylinder and cutting squish to some minimal dimension. Will these low cost components stand up to high compression, etc., I don’t know….. I’d come across a few of you experienced builders who shared numbers, and set out to replicate port timings that Mastermind shared in a post a number of years ago (102, 126, 81.X).
Stock numbers w/o base gasket measured 98, 130.5/133, 77.5, squish .036. I took .036 off the cylinder base and landed on Mastermind’s timing numbers. I then made a squish cutting tool and sanding drum as Treemonkey showed in a video (thanks Treemonkey, I’m about 60miles south west of you). And even though I was cautioned to not create a ridge that can falsely show a big squish reading, I let it happen. I hadn’t ground enough relief at the end of my tool bit. By the time I corrected that and got the ridge cut out, I was right back at the stock .036” squish.…..
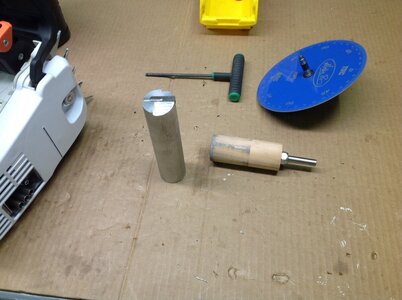
So I took another .019” off the base, knowing the intake duration would end up greater than the target, but I figured I had really nothing to loose and experience to gain. Not wanting to recall the math needed to calculate port height vs degrees, I made a simple model in Solidworks using the stroke and rod length. From this model I determined the primary and secondary transfers should be raised .089 and .079 respectively, to land on 126/129 degrees.
The open transfer design allowed me to grab the cylinder upside down in the mill vice and accurately cut them “deeper” (and keep them flat) by those dimensions, using a 1/4” carbide end mill. I attempted to blend the remaining step into the corners of the transfer ports, making a small radius there with an 1/8” dremel bit (I hated to show pic of this work!). I raised the exhaust a bit and slightly widened the exhaust and intake to end up with these timing numbers:
EX 102
pri 126
sec 130
IN 82.5
I, more carefully this time, cut the squish to .019”. The muffler outlet I made with 3/8” OD tubing. I used three of these outlets to land on a combined area I’m hoping will run well. I have not yet measured compression, but am guessing it’s fairly high. Piston is a Hyway pop-up. I have no bar yet so only ran it w/o load this morning. The throttle response seems good and it is “very angry” in nature. Am looking forward to getting it in some wood.
Possible concerns:
Will the cheap crank ass’y and bearings take it?
After removing .055” from the cylinder base, the flange thickness is only .155”. Will it fracture there?
Is the resulting 165 degees intake duration likely to cause poor performance and/or waste fuel?
Is the width of the squish band too great (or the dome volume too small)?
Will I be sucked into yet another hobby where no number of chainsaws will ever be enough?
Thanks for reading!
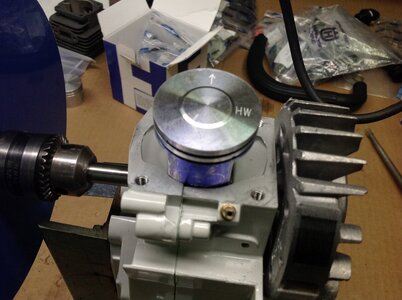
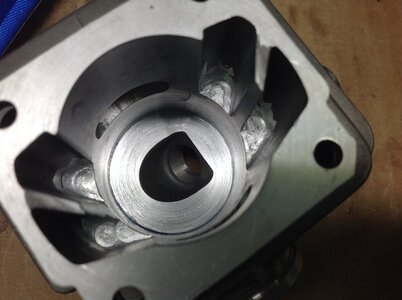
Last edited: