Backtroller
Here For The Long Haul!
- Local time
- 10:00 PM
- User ID
- 349
- Joined
- Dec 31, 2015
- Messages
- 2,791
- Reaction score
- 11,312
- Location
- Land of Badgers

What works the best for me is to cut the hose in half so you have two. I removed the pump and bolt it to side if my workbench through the bolt holes. I put a little oil inside of the hard black hose and get out the heat gun. Once the plastic pipe is hot enough I took a 1/2" copper water pipe cap and put that over the end of the piece and push firmly down. I chamfered the opposite end that goes to bar so it goes a little more smoothly through that hole. But before you attempt to put it in the hole put the spring inside of the hose. After you get it all in it will be a little long and I just trim as square as I can with an exacto knife and push in the brass piece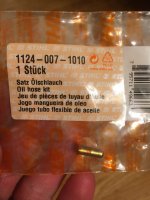
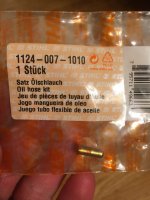