XP_Slinger
They’re Just Saws
- Local time
- 8:15 PM
- User ID
- 845
- Joined
- Feb 9, 2016
- Messages
- 6,089
- Reaction score
- 27,523
- Location
- Central NY

Bought this 394 as a project saw last year. Had a bad carbon smear on the piston and cracked flywheel side crank case. It ran good so I cleaned the carbon off the piston and ran it for a year.
Well, the carbon smear returned and looked much worse. Looked like it was starting to transfer, time for a rebuild. Note the polish and port shadow on the exhaust skirt, piston is well worn and long overdue for replacement. This isn’t going to be a PSP shelf queen rebuild, if it’s not broke I’m not fixing it, if it’s ugly I don’t care. This saw is going to work.
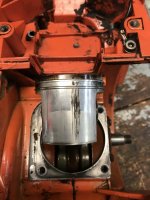
Here’s the crack in the case. Saw passed Pressure and Vacuum test, but who likes cracked cases...time to swap it out.
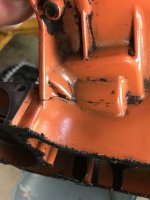
Edit: photos don’t illustrate the order in which I assembled the saw, was waiting on some small parts til late in the day.
Well, the carbon smear returned and looked much worse. Looked like it was starting to transfer, time for a rebuild. Note the polish and port shadow on the exhaust skirt, piston is well worn and long overdue for replacement. This isn’t going to be a PSP shelf queen rebuild, if it’s not broke I’m not fixing it, if it’s ugly I don’t care. This saw is going to work.
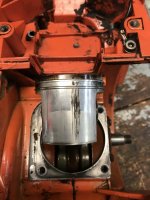
Here’s the crack in the case. Saw passed Pressure and Vacuum test, but who likes cracked cases...time to swap it out.
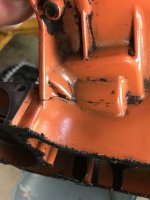
Edit: photos don’t illustrate the order in which I assembled the saw, was waiting on some small parts til late in the day.
Last edited: