chy_farm
Pinnacle OPE Member
- Local time
- 7:36 AM
- User ID
- 3497
- Joined
- Jul 3, 2017
- Messages
- 397
- Reaction score
- 2,126
- Location
- Yokohama, JAPAN
This is a bunch of short reports on how I tried fabricating a CDI(Capacitor Discharged Ignition) unit for an old Partner saw on my own.
See some videos;
Homemade CDI unit for Partner R417T(I), a test run!
Homemade CDI for Partner R417T (II)
Homemade CDI for Partner R417T (III)
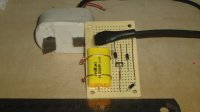
The circuit is very simple, with only several parts on the board.
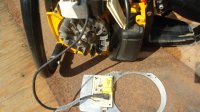
Will post some reports on her later.
Chy
See some videos;
Homemade CDI unit for Partner R417T(I), a test run!
Homemade CDI for Partner R417T (II)
Homemade CDI for Partner R417T (III)
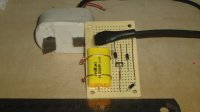
The circuit is very simple, with only several parts on the board.
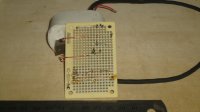
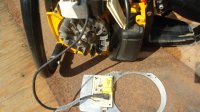
Will post some reports on her later.
Chy