Pretty easy really, just tig a bead around to build it up, then machine to spec.
I usually profile them into a sort of bell curve rather than the abrupt bevel and flat top.
Contamination/porosity is the one issue that, as with any welding, can sometimes be a pain.
I was playing around with a surplus of 350 pistons leftover from 353 flattop upgrades,
filling in the dish to make them flat. Added around 3 grams of weight.
One thing I ran into there was overheating and collapsing portions of the ring groove,
normally not an issue with welded popups because you're not that close to the edge.
Did popups on a couple cause why not since I'm welding/machining anyway.
Distortion of other parts of the piston didn't seem to be a problem.
One odd thing was that a couple of them made less compression than expected, I'm thinking the ring groove issue was somehow at play there even though the ring seemed to fit fine.
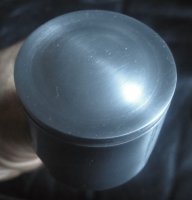