super3
Pinnacle OPE Member
- Local time
- 2:00 AM
- User ID
- 358
- Joined
- Dec 31, 2015
- Messages
- 355
- Reaction score
- 1,297
- Location
- Indiana

Ya I know what the fk is a crank tread? One of you mods change the spelling for me.
I've had to repair the threads on several cranks over the years for whatever reason they were damaged. Ham fisted flywheel removers, piss poor packaging and dropped in shipping, flywheel remover used with nothing to keep the end of the crank threads from getting mushroomed and one I fked up and knocked off the bench.
After checking to make sure they still run true this was the simplest way that I have come up with to get a re thread die to start right and not make things worse than what I started with.
1st I use a sanding roll to take out the bulge on the end and give it a bit more taper.
2nd I file just a bit any spots where the threads were pushed together and would not let a die start.
3rd I hacksaw a slot in a nut(grade 8 or better), drive a carb screwdriver in the slot to expand it ( this gives it enough clearance to get over the f'ed up threads) and thread it on the crank far enough to get to the good threads. Remove the screwdriver and use a small pair of vise grips on the flats to put just a bit of drag on the nut.
Work it out to the buggered up part of the threads and turn back and forth about a 1/4 turn at a time until you feel it getting easier to turn and keep working your way to the end of the crank. Back it up periodically and blow off the small shavings.
The slot that was cut in the nut also creates a bit of a softer cutting die as of sorts, just enough to let you shave the threads to get a re thread die started on correctly. If it won't start easily repete step 3 until it does.
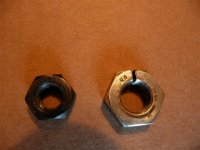
I've had to repair the threads on several cranks over the years for whatever reason they were damaged. Ham fisted flywheel removers, piss poor packaging and dropped in shipping, flywheel remover used with nothing to keep the end of the crank threads from getting mushroomed and one I fked up and knocked off the bench.
After checking to make sure they still run true this was the simplest way that I have come up with to get a re thread die to start right and not make things worse than what I started with.
1st I use a sanding roll to take out the bulge on the end and give it a bit more taper.
2nd I file just a bit any spots where the threads were pushed together and would not let a die start.
3rd I hacksaw a slot in a nut(grade 8 or better), drive a carb screwdriver in the slot to expand it ( this gives it enough clearance to get over the f'ed up threads) and thread it on the crank far enough to get to the good threads. Remove the screwdriver and use a small pair of vise grips on the flats to put just a bit of drag on the nut.
Work it out to the buggered up part of the threads and turn back and forth about a 1/4 turn at a time until you feel it getting easier to turn and keep working your way to the end of the crank. Back it up periodically and blow off the small shavings.
The slot that was cut in the nut also creates a bit of a softer cutting die as of sorts, just enough to let you shave the threads to get a re thread die started on correctly. If it won't start easily repete step 3 until it does.
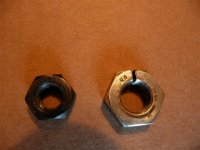