thompsoncustom
Well-Known OPE Member

well was playing around this putting stuff in the combustion chamber on my ms260 and ended up casting some aluminum and holding it in with a bolt and using jb weld as a gap filler.
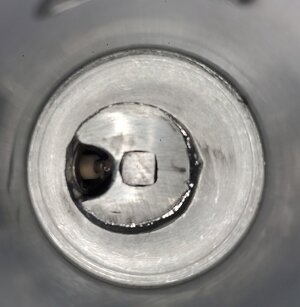
compression came in at 245psi before breakin it in. after about 5 mins of run time the insert failed from to much pressure getting behind it.
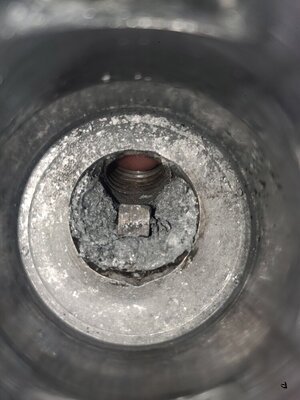
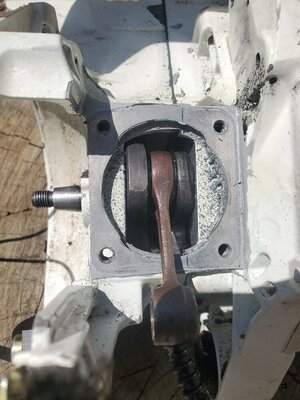
there was aluminum everywhere exhaust and case were full I even found some in the air filter. but after cleaning everything up and flushing everything out I'm going to continue testing with all the same parts.
used some red scotch brite by hand in the cylinder.
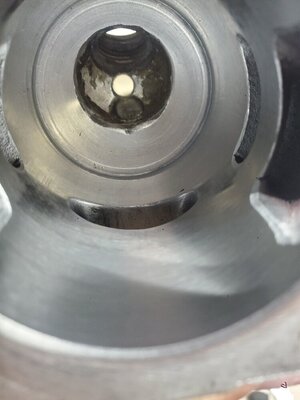
just thought I would share since I didn't ever image it would survive.
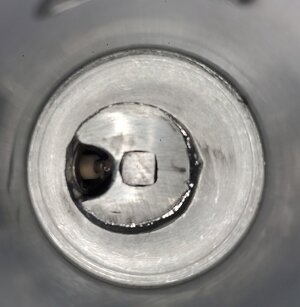
compression came in at 245psi before breakin it in. after about 5 mins of run time the insert failed from to much pressure getting behind it.
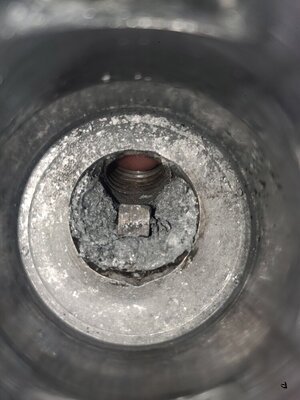
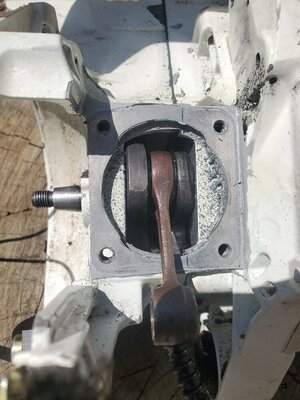
there was aluminum everywhere exhaust and case were full I even found some in the air filter. but after cleaning everything up and flushing everything out I'm going to continue testing with all the same parts.
used some red scotch brite by hand in the cylinder.
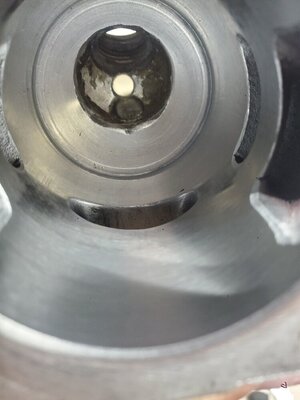
just thought I would share since I didn't ever image it would survive.