NPKenny
Super OPE Member
- Local time
- 1:02 PM
- User ID
- 5030
- Joined
- Jan 12, 2018
- Messages
- 292
- Reaction score
- 743
- Location
- Lehi, AZ

I could use some help with the process of machining the backing plate for my 4-jaw chuck.
It’s my understanding that the benefit of a blank backing plate is that it can be basically machined as part of the lathe to be perfectly true.
I would appreciate any tips on process order, rpm, tooling, etc. Should the mounting holes be tapped, or through holes? Do I tap them before or after indexing? The plate looks to be cast and it is not well indexed to the chuck. The chuck has never been mounted.
I’ve posted this in the chainsaw forum since cutting squish bands and bases was the motivation for learning how to use a lathe.
Thank you!
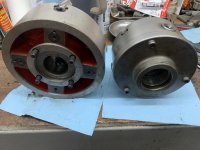
It’s my understanding that the benefit of a blank backing plate is that it can be basically machined as part of the lathe to be perfectly true.
I would appreciate any tips on process order, rpm, tooling, etc. Should the mounting holes be tapped, or through holes? Do I tap them before or after indexing? The plate looks to be cast and it is not well indexed to the chuck. The chuck has never been mounted.
I’ve posted this in the chainsaw forum since cutting squish bands and bases was the motivation for learning how to use a lathe.
Thank you!
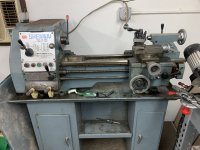
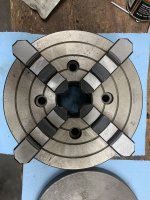
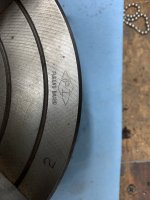
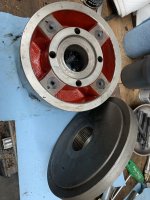
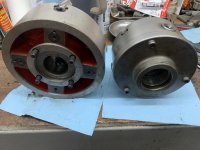