Steelie90
Well-Known OPE Member

064 on the bench, cut the chamber and then base to get my desired squish. Landed on .023 PTO .0235 flywheel, l checked 1 side at a time.
I seen a post recently where squish was checked using 2 small pieces greased to the piston. I liked the idea, eliminate “rock” in the piston and bearing tolerances. So I thought I would check that way also. After doing that it came out .017 both sides.
Pretty surprised by the difference.
This is with new crank bearings and wrist pin bearing installed. This piston does have skirt wear and cylinder is well used, which I’m sure could contribute to the vast difference in readings. But I was still surprised. Makes me concerned about a few saw I built with squish at .020 checked 1 side at a time.
How do you do it? I’m thinking I will change my way from here forward. Few build pics. Forgot to take some of squish process.
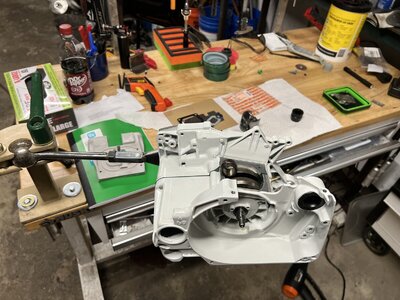
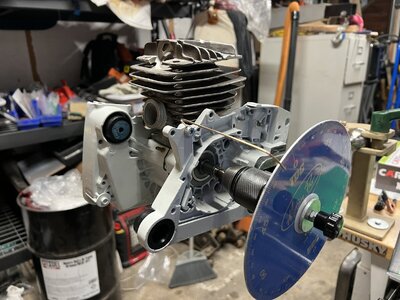

I seen a post recently where squish was checked using 2 small pieces greased to the piston. I liked the idea, eliminate “rock” in the piston and bearing tolerances. So I thought I would check that way also. After doing that it came out .017 both sides.
Pretty surprised by the difference.
This is with new crank bearings and wrist pin bearing installed. This piston does have skirt wear and cylinder is well used, which I’m sure could contribute to the vast difference in readings. But I was still surprised. Makes me concerned about a few saw I built with squish at .020 checked 1 side at a time.
How do you do it? I’m thinking I will change my way from here forward. Few build pics. Forgot to take some of squish process.
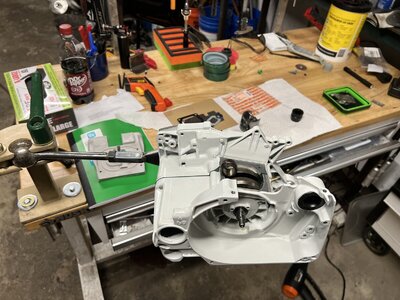
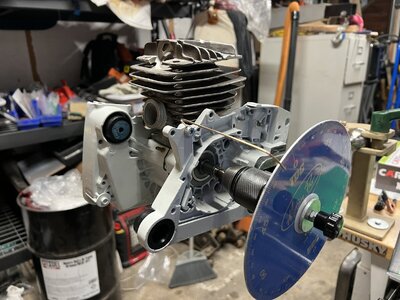
